The factor related to lubrication that affects the accuracy of the operation of the electric spindle is the heat generated by the electric spindle. The internal heat source of the electric spindle comes from two aspects: 1. The heat of the spindle bearing; 2. The heat generated by the built-in motor of the electric spindle.
Solving the heating of the motor requires cooling the stator of the motor. It can be realized by circulating water cooling method to take away the heat of the motor. To solve the heating problem of the spindle bearing, it is necessary to take away the heat generated by the bearing operation in time. The traditional thin oil lubrication is to transport a large amount of lubricating oil to achieve invasive lubrication, and at the same time, the lubricating oil takes away the heat. There are disadvantages in such a lubrication method. One is to waste a large amount of lubricating oil, and the other is that the lubricating oil is rubbed between the lubricating oil molecules and the pipe to generate a large amount of circulating heat during the circulation, resulting in an increase in oil temperature. Not only can not play a good cooling effect, but also lead to an increase in bearing temperature, which is not conducive to the performance of the spindle bearing. Therefore, eliminating the generation of frictional heat between molecules inside the liquid becomes the key to solving the problem. Practice has shown that oil and gas lubrication can fundamentally avoid this situation. First, oil and gas lubrication provides a small amount of lubricant to meet the amount of lubricant required for the bearing. Secondly, the oil and gas lubrication does not cause the friction of the lubricating oil molecules to generate heat, and the clean compressed air takes away the heat generated by the bearing, keeping the spindle running at a stable temperature. This can effectively solve the problem of thermal deformation caused by an increase in temperature.
Dopo is committed to the research and development of electric spindle oil and gas lubrication for many years. With mature oil and gas lubrication products and rich application experience, it will bring more value to customers.
Doppler's electric spindle oil and gas lubrication has the following advantages:
1,
The electric spindle bearing chamber can obtain a positive pressure environment to prevent the intrusion of external impurities.
2. Compressed air can provide good cooling effect on the bearing.
3,
Lubrication points for independent working at 1-8 points, reliably monitoring the oil supply situation of each lubrication point.
4. The consumption of lubricating oil is controlled by precise metering, so the consumption is very low.
5,
Modular structure, which can increase or decrease the module components according to the number of lubrication points to achieve multi-point combination;
6, complete electronic program control, quick setting through convenient man-machine interface;
7. The oil and gas lubrication equipment is easy to operate and has low maintenance costs.
Doppler electric spindle oil and gas lubrication device has: precise and parameterized operation of oil supply, easy operation, and system monitoring of liquid level, gas source pressure and flow output. At present, it has been used for multi-home appliance spindle manufacturers.
High Purity Nitrogen Generator is one kind of skid nitrogen can produce nitrogen with purity up to 99.9999%. This Nitrogen Generator includes one 99.5% purity nitrogen generator and one 99.999% purity nitrogen purifier. It is a good way to achieve high purity nitrogen with low energy consumption. It is easy for ocean transportation, no need for site installation. When machine reach site, just need to put the machine on flat ground, connect power and gas pipeline, then one simple push on starting button makes the nitrogen generator begin to work.
Step one: 99.5/99.9% purity nitrogen generator
This nitrogen generator is the Standard Nitrogen Generator supplied by Gamma. It has Air Compressor , air treatment part, air tank, nitrogen separator and nitrogen buffer tank. It is normally installed on one skid, so this nitrogen generator is also called Skid Nitrogen Generator. After this purity nitrogen is produced, the nitrogen goes to nitrogen purifier.
Step two: nitrogen purifier
The principle of nitrogen purifier is adding hydrogen or carbon to the produced nitrogen. In this way, the oxygen acts with hydrogen to generator water and oxygen is removed. Chemical formula is as below:
2H2+O2==2H2O+Q
During the process of removing oxygen, water will be generated. In order to reduce the dew point of produced nitrogen, there are cooler, Adsorption Dryer , filtration dust removal devices in the system, used to remove water, dust, etc to get high purity clean nitrogen.
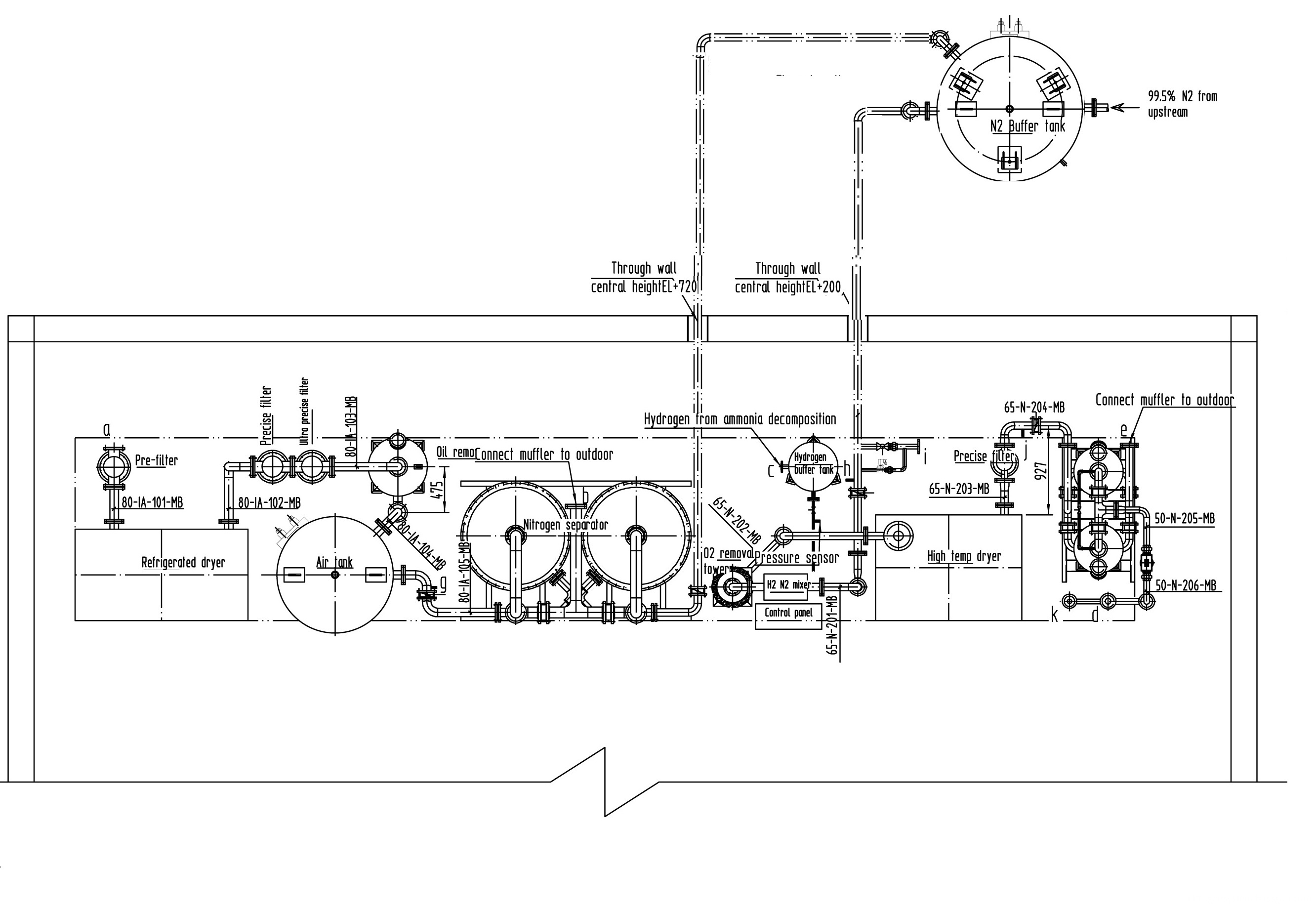
High Purity Nitrogen Generator
High Purity Nitrogen Generator,High Purity N2 Generators,High Purity Psa Nitrogen Generator
Shandong Gamma Gas Engineering Co. Ltd. , https://www.gammagas.com