- Model No.: JZQ-18
- Usage: Sheet, Wire, Pipe, Bar
- Automatic Grade: Semi-Automatic
- Certification: ISO9001
- Customized: Available
- Trademark: QIPANG
- Specification: 400mm x 120mm x 120mm
- HS Code: 8463102000
- Type: Pressure Leveler
- Voltage: 220V
- Principle: Small Deformation
- Warranty: 12 Months
- Condition: New
- Transport Package: Box, Carton, Wooden Crate
- Origin: Shanghai, China
Specifications
The wire straightener is primarily used on drawing machines and comes in single or dual plane models. It features an eccentric roller open/closing device (lever) with 5 to 13 rollers per group (e.g., 5, 7, 9, 11, 13 or 5+5, 7+7, etc.). Roller diameters range from 13 mm to 80 mm (0.5" to 3.15"). The upper row of rollers is adjustable, and the machine offers options for light or heavy-duty applications.
For example, model AS/AD is suitable for wires with a tensile strength of up to 60 N/mm² (8400 psi) using standard rollers. The straightening wheels typically have "V" grooves, but can also be customized with "U" grooves upon request. A wire guide is included as standard.
The lettering in the model name, such as JZQ---5/49, indicates: "J" stands for straightener, "5" refers to the number of alignment wheels (18 in this case), "49" is the diameter of the straightening wheel, "A" denotes the overall opening and closing design, "B" means independent adjustment of a single roller, and "T" represents a special type of straightening device. The groove type can be V, R, U, or custom-made.
This machine is equipped with 26 rollers, each with a diameter of 22 mm, specifically designed for welding wires. During the straightening process, the rollers are positioned to move the product in a specific direction. Two or three large pressure rollers drive the rotation, while smaller rollers apply friction against the rod or pipe. These small rollers can adjust their positions simultaneously or individually forward or backward, ensuring higher precision with more rollers.
The product undergoes continuous linear or rotational motion, experiencing compression, bending, and flattening deformation, ultimately achieving a straightened result. Below are some images of the 18-roll automatic straightening device with feeder system.
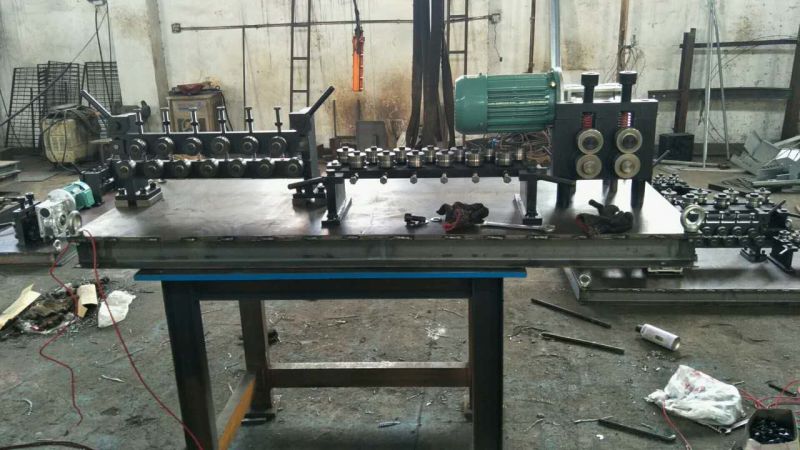
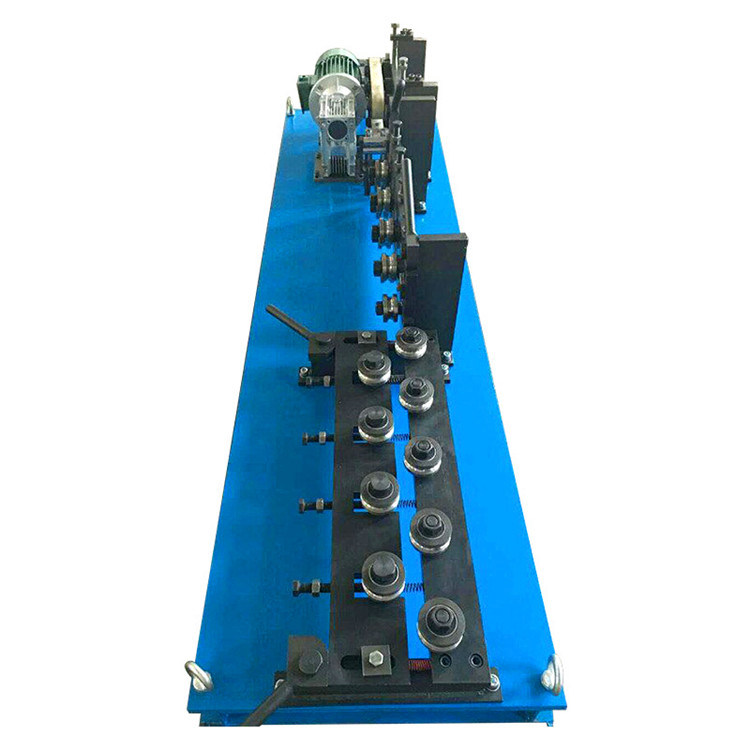
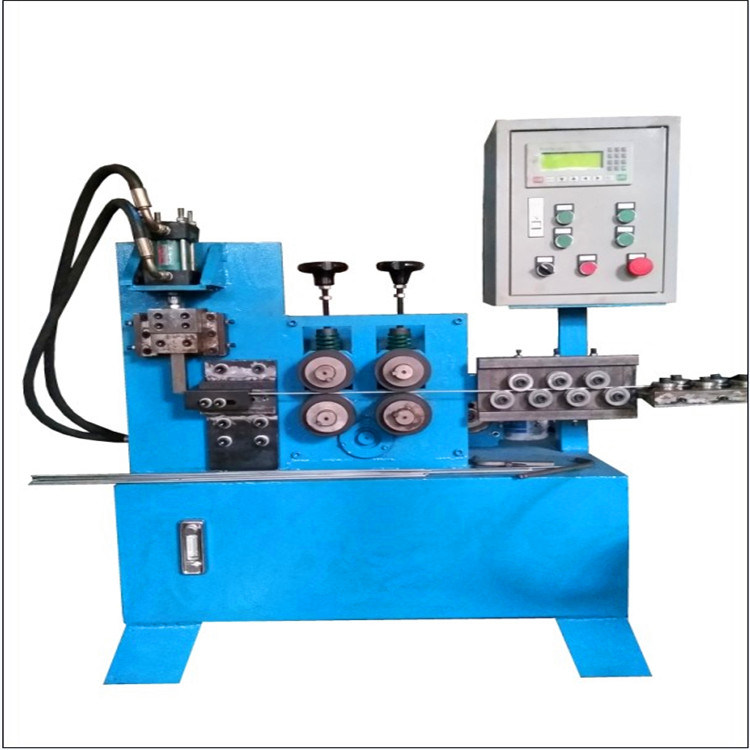
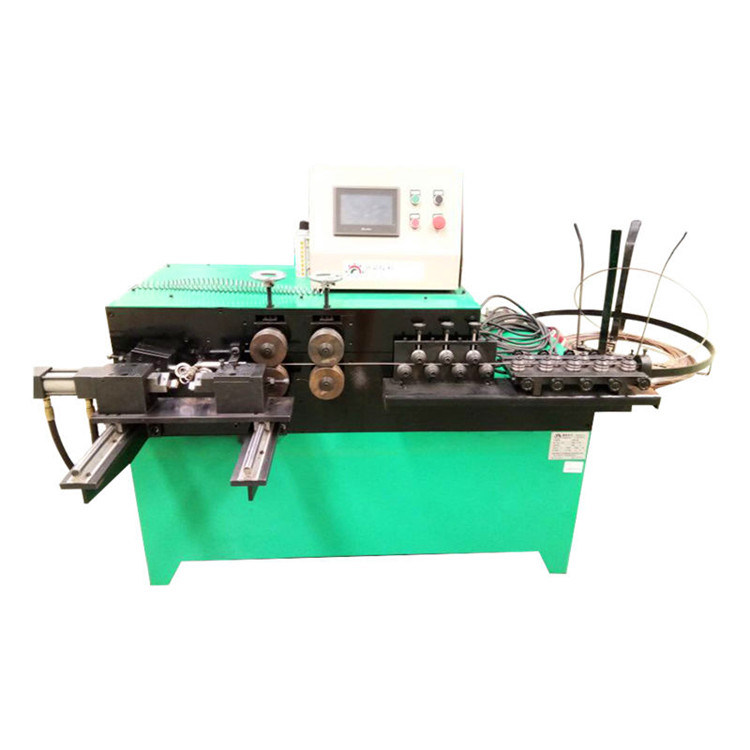
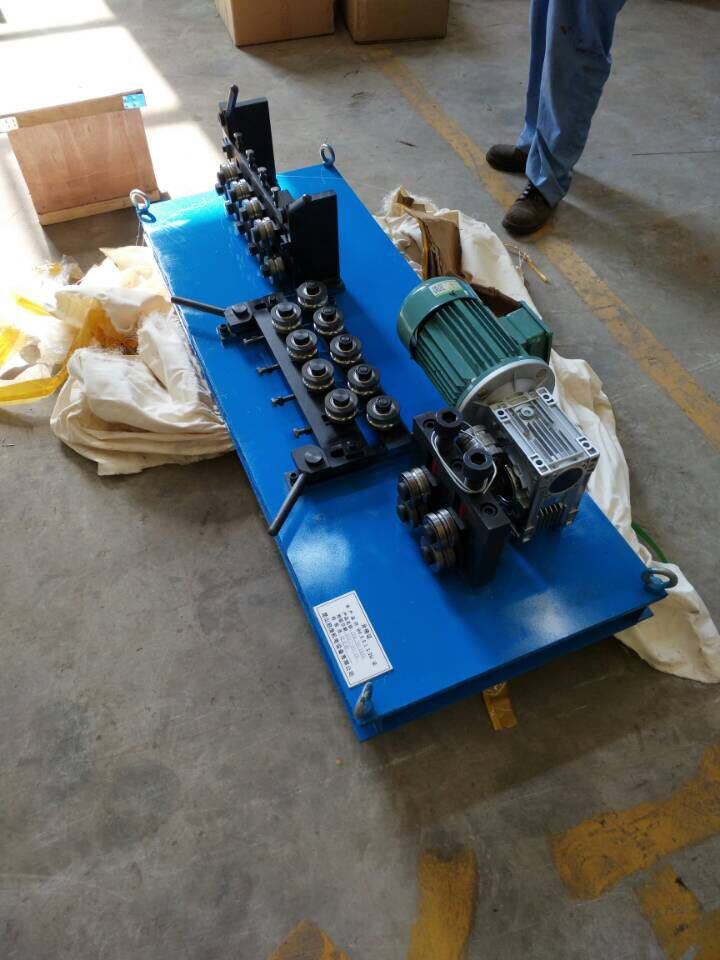
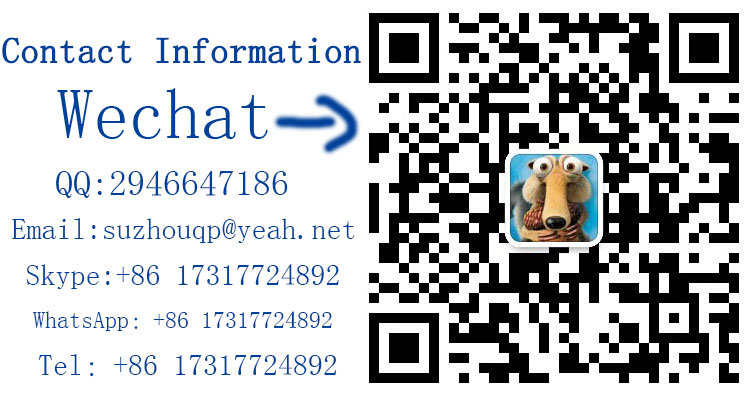
Multilayered Pipe Co-extrusion Production Line
Plastic Co-extrusion Machine,Plastic Multi-layer Extrusion line,Plastic Extrusion Machine
Zhangjiagang Polestar Machinery Co.,Ltd , https://www.polestarpm.com