Introduction In recent years, the University of Texas at Austin has been conducting research on separation projects. When it comes to process modifications, new measurement points need to be added to the relevant process equipment and the process flow is tested. It was found in the experiment that when the measuring point was increased or changed, the time required to start and stop the process was three times longer than the actual time. Therefore, it was the most important to reduce the instrument installation time and plant downtime. Since no cabling or rewiring is required, the wireless transmitter offers great flexibility for reconfiguring process points.
Process Equipment In order to evaluate the performance of wireless transmitters in control applications, we have specifically installed a device that is currently used to test energy-saving stripping processes associated with carbon dioxide capture in thermal power plants. From the process point of view, it includes an absorption tower to remove carbon dioxide from the simulated stack gas stream by ammonia solvent, and then reduce carbon dioxide through the stripping column, and recover and reuse the regenerated ammonia solution in the absorption tower. The figure on the right is the device.
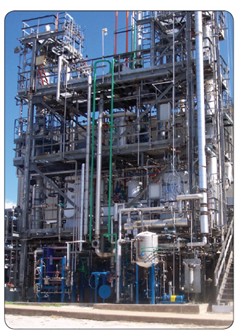
Absorption towers mainly test specific solvents and packings or tray internals. The absorption tower has two 10-foot packed beds. The liquid collector and liquid redistributor are located in the middle of the tower. In the separation research program there is a carbon dioxide collection experiment in which ambient air is mixed with recycled stripped carbon dioxide and make-up carbon dioxide enters from the bottom of the tower. When the air stream flows upwards through the packing, carbon dioxide is absorbed by the downward flowing liquid ammonia. The resulting solution is called an ammonia rich solution and enters the stripping section to remove the absorbed carbon dioxide.
The stripper mainly tests the filler and determines the energy efficiency of the specific solvent. There are also two 10 foot long packed beds in the tower. The liquid collector and liquid redistributor are located in the middle of the tower. The solution coming out of the absorption column is called a monoethylamine saturated solution and is heated together with the liquid at the bottom of the stripping column through a cross-flow plate exchanger and then injected into the top of the stripping column. The steam generated by the kettle reboiler can separate part of the carbon dioxide. The distillate at the top of the tower enters the tube condenser, the steam condenses in the condenser, and the lean ammonia returns to the feed tank of the absorption tower.
Wireless devices installed in the process industry for wireless field devices have undergone rapid development after several years of development and design. After analyzing existing wireless technologies, we decided to use wireless HART compliant wireless devices in the fractionation research program. Wireless pressure and differential pressure transmitters are used in control loops that control tower pressure and vapor flow.
The WirelessHART Wireless Gateway is installed in the middle of the process unit area and is connected to the control system via Ethernet. The control system uses a DeltaV system that integrates the standardization of the system with the wireless gateway to implement WirelessHART instrument verification, configuration and diagnostic functions. The configuration method of the wireless instrument in the control system is the same as that of the traditional instrument. The difference is that the wireless instrument is powered by the battery and no power cable is required to be installed.
We changed the original tower pressure and steam flow control modes, and now operators can switch between wired and wireless inputs. When a control loop input signal is implemented by a wireless meter, the system will automatically change the PID module to wireless control. The instrument panel can display the currently selected input signal type and selector switch position so that the operator can be intuitive through the display interface. Compare the measurement results of wired and wireless solutions and select either wired or wireless signals as control loop inputs at any time.
We added a matrix diagram to the control model to calculate the automatic control absolute error integral (IAE). The control loop measurement values ​​and control cycles are automatically recorded to compare the performance of the control loop using wired and wireless solutions.
Test Procedure In a recent packing performance test, a preliminary test of the wireless pressure transmitter and differential pressure flow transmitter was conducted to test the distillation efficiency and hydraulic performance of the Raschig-Jaeger RSP-250 packing ( The stripper can also be used as a distillation column). Fractionation towers are fractionated by a cyclohexane/n-heptane blending system. The effect of pressure on distillation performance is also within the scope of the study. The standard test pressures are 2.4, 4.83, 24, and 60 psia. For wireless instrumentation, the base pressure is 24 psia. Raschig-Jaeger Company agreed to apply wireless instruments for testing during the operation of the experiment.
Table 1 shows the pressure control achieved by the wired meter and the wireless meter on the dephlegmator. In the experiment, the PID tuning parameters, filter parameters, and control configuration parameters were set the same. The results are shown in Table 1. There is no difference in the performance of the two schemes.
Control performance:
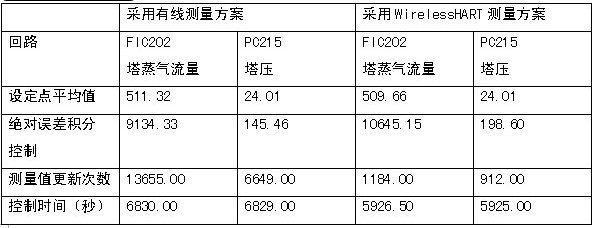
Table 1: Wired and wireless control results are comparable
We also obtained similar results in the test of steam flow control. The filtering time of the wired instrument is 10 seconds, and the wireless instrument is 0 seconds. The factory's original PID tuning can be applied to both wired and wireless instruments. When the set point is changed, the same dynamic control can be seen.
According to the graph, from the standpoint of the absolute error integral measured in the pressure control and steam flow control of the wireless instrument application, the wireless instrumentation has the same control performance as the wired instrument, and the wireless control loop only uses 1 compared to the wired one. The /10 quantity of measured values ​​is used for flow control, and 1/6 of the measured values ​​are used for controlling pressure, thus saving battery energy consumption.
The test results show that the application of the WirelessHart wireless transmitter combined with the modified PID algorithm function module achieves the same control reliability as the traditional hard wired transmitter and the standard PID algorithm. In another test, the composition and packing efficiency measurements (theoretical plate height) were performed using a conventional hard-wired transmitter, and then the same operation was performed using a wireless transmitter. The results showed that the control performance of both was almost the same.
Performance comparison:
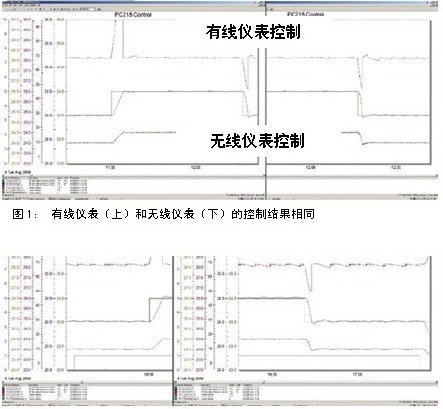
Extended Applications WirelessHART wireless transmitters to measure air flow and tower pressure save on cabling costs. The use of WirelessHART transmitters and a modified PID algorithm function block for tower pressure and heater steam flow control enables the dynamic response and performance to be exactly the same as wired meter plus traditional PID calculations.
During the experiment, we extended the application of WirelessHART technology by first using three multi-point wireless temperature transmitters (each device has four thermal resistance inputs) to monitor the temperature distribution of the absorption tower, and to add two more Wireless pH transmitters are installed at the inlet and outlet of the absorber, respectively, to indirectly measure the concentration of carbon dioxide in the ammonia solution. The use of wireless transmitters improves the accuracy and reliability of temperature and pH measurements, thereby improving the operating conditions of the stripper and absorber. Because the wireless meter is powered by batteries, the effects of grounding the wired instrument loop are eliminated.