Abstract: In this paper, a pharmaceutical project in the south is used as an example to introduce the process characteristics, parameters detection and control methods in the contemporary pharmaceutical fermentation process. The project adopts DCS control system to achieve automatic control of temperature, pressure, dissolved oxygen, PH value, flow rate, etc., and uses historical data records to achieve records such as historical report query and history curve query, providing a reliable basis for accident recovery.
1 Introduction:
The use of secondary metabolism in the growth of microorganisms to obtain antibiotics in the pharmaceutical industry is a major creation of human biotechnology. This metabolic process is completed in the fermenter during industrial production. An in-depth study of the fermentation process will lay the foundation for the biochemical reaction—the design, operation and control of the fermenter. Therefore, it is one of the important contents of improving the level of biochemical engineering; biochemical reaction is a difficult point in biochemical technology. In the research and practical application, it needs not only microbial technology but also borrows chemical technology and modern measurement technology, computer technology and control technology. One. The microbial fermentation process is an extremely complex biochemical reaction process. For the operation of the fermenter, people used to rely on practical experience to conduct the operation. Due to the lack of measurement monitoring and control system of the fermentation process parameters, the fermentation product cost is high and the operating cost is high. The lack of competitiveness in the international market requires the optimization and control of fermentation tanks. Especially with the development of various technologies of computer control systems, distributed control systems have become more widely used in the pharmaceutical industry. This article mainly describes how to use distributed control systems to optimize the pharmaceutical control program.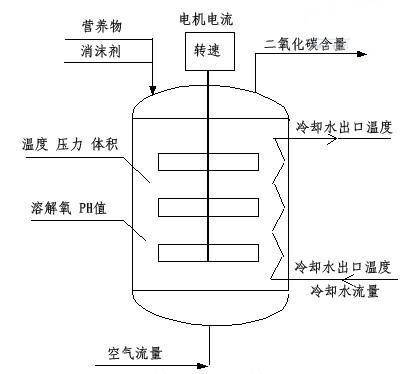
Figure 1 fermentation tank detection parameters
2, the process of fermentation and its characteristics The general oxygen-consuming fermentation tank system shown in Figure 1, which parameters to be measured can be divided into physical parameters, chemical parameters and biological parameters.
2.1 The physical parameters of the fermentation process are usually the fermentation tank temperature (T), the fermentation tank pressure (P), the fermentation liquid volume (V), the air flow (FA), the cooling water inlet and outlet temperature (T1¬ and T¬2) and the flow ( FW) stirring motor rotation speed (RMP), stirring motor current (I), foam height (H), etc. These physical parameters can be selectively selected to achieve automatic measurement according to different types of fermentation requirements.
2.2 Chemical parameters of the fermentation process:
The typical chemical parameters of the fermentation process are pH (PH) and dissolved oxygen (DO). These two parameters are very important for the growth of microorganisms and the formation of metabolites.
2.3 Fermentation process biological parameters:
Biological parameters typically include biomass respiratory metabolic parameters, biomass concentration, metabolite concentration, substrate concentration, and bio-specific growth rate, substrate consumption rate, and product formation rate. Regarding biological parameters, there are few real-time on-line measuring instruments in industrial production, both at home and abroad. It is precisely for these reasons that the control of the microbial fermentation process is more difficult than the general industrial production process.
3. Control of fermentation process With the rapid development of bio-industrial technology, its production equipment and scale are continuously expanding, the production process is strengthened, the requirements for automatic control technology are more and more urgent, the optimal control of the biochemical process is implemented, and production can be stabilized. Improve the yield, reduce consumption and increase efficiency. However, the microbial fermentation process is different from the general process industry. Because it involves the growth and reproduction process of living organisms, the mechanism is very complex, and various unpredictable oscillations often appear in the fermentation process, which brings about optimal control of the fermentation process. Great difficulty.
3.1 Conventional control of fermentation tank temperature For a given microorganism, it has an optimum growth temperature. If considered from the point of view of the enzyme kinetics, the best activity of the enzyme corresponds to the best temperature. Therefore, the control of the fermentation temperature in the microbial fermentation process is a very important environmental parameter for microbial growth and must be strictly controlled. The main factors affecting the fermentation temperature are the temperature of the microbial fermentation heat, the motor's stirring heat, and the cooling water itself.
The small-scale fermentation tank temperature control system is a single loop control scheme in which the fermentation tank temperature is controlled and the cooling water flow rate is a control parameter. For a large-scale fermentation tank system, the fermentation tank temperature is used as the main circuit, and the cooling water system is used. Cascade control or feedforward-feedback control scheme for the secondary loop.
(1) Single-loop PID control In the case of stable inlet water temperature, the temperature of the fermentation reaction tank is often controlled by a single loop PID. In the actual process of industrial fermentation process temperature control, due to changes in cooling water (or warm water) temperature, will affect the fermentation temperature control quality, the impact of the process is to first change the jacket temperature, and then change the temperature of the fermenter, only At this time, the controller senses the temperature difference and drives the regulator. Obviously, from the beginning of the disturbance to the action of the regulating valve, a large lag is required. To overcome these lags, cascade adjustment can be used.
(2) Cascade control The signals measured by T1 and T2 are combined into a control system. The output of TC1 is used as the reference value of the TC2 controller to form a cascade control system. Compared with single-loop control, cascade control has the following features:
(1) When the jacket temperature fluctuates due to some outside reason, the effect of TC2 will make this fluctuation overcome before it affects T1, so it is beneficial to ensure the control quality of T1. It can significantly improve the control characteristics of the fermenter and reduce the equivalent object lag.
(2) Two parameters can be taken into account to achieve "uniform control: When the main controller TC1 has a wider selection of proportionality, its output changes less. Because it is a given value of the sub-controller TC2, it makes secondary parameters. The change is also relatively small and relatively stable, so that the two main and auxiliary parameters can be kept within a certain range of fluctuations to meet the requirements of the process.
(3) The influence of non-linear characteristics such as the control valve can be eliminated: Since the control valve and a part of the object (sub-control object) are included in the sub-circuit, the nonlinear influence of the control valve is eliminated in the sub-ring.
(3) Feedforward-feedback control The cooling water temperature disturbance signal is applied to the regulating valve together with the output signal of the TC1 controller to form a feedforward-feedback control, so that the disturbance of the cooling water temperature change can be achieved. Quickly acting on the regulating valve, the regulating valve is also adjusted accordingly to eliminate this disturbance in time, but it should be noted that the feedforward compensator needs to have an accurate mathematical model as a basis.
3.2 Fermenter pressure The conventional control of the pressure change in the fermenter will cause the partial pressure of oxygen to change in the fermented liquid, which will affect the change of dissolved oxygen concentration. In addition, in order to prevent the fermentation product from being infected by bacteria, it is necessary to filter and sterilize the introduced compressed gas, and to ensure positive pressure in the fermentation tank so as to prevent the entrance of external untreated air and the like. The pressure that affects the fermenter is mainly the pressure change of the supplied sterile air. Usually the control of the pressure in the fermentor is controlled by adjusting the amount of exhaust gas. Generally, single-loop control can be used. The influence of the pressure change in the fermenter on the dissolved oxygen concentration is treated by the dissolved oxygen concentration control loop. Of course, the adjustment of the dissolved oxygen concentration will take into account the influence of the pressure in the tank.
3.3 pH Control During Fermentation PH is another important environmental parameter for microbial growth. In the fermentation process, it must be strictly controlled, otherwise it will seriously affect the metabolism of microorganisms and the synthesis of metabolites. In industrial production, if the PH value of fermentation broth is low and the ammonia nitrogen is also low, the PH value is increased by adding ammonia water, etc.; if the PH value is high and the ammonia nitrogen is low, ammonium sulfate or chlorination can be added. Ammonium; If the PH value and ammonia nitrogen are both high, in the early fermentation stage, the amount of sugar can be adjusted to increase. There are generally no other controls. Therefore, in the pH value control, the amount of the adjustment liquid must be strictly controlled and must not be excessive. As shown in FIG. 2, the pH value is controlled by the pH measuring electrode and the transmitter, the PH controller, the air switch, and the pneumatic switch valve. composition.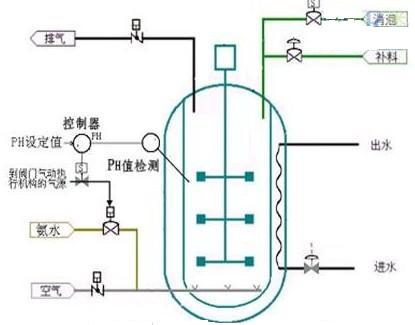
Figure 2 PH value control flowchart
Ammonia can be added to the fermentor through the sprinkler head. Of course, it is best to send it to the fermenter through the air duct together with the air, so that the ammonia can be fully distributed in the fermentation broth without causing high or low pH in the local area. . In order to avoid the defect that the general control valve has a leakage amount, in the PH control, the used valve is a commonly used on-off valve. According to the PH deviation signal, the controller calculates the switching period and the length of the opening and closing of the switching valve to control the amount of the adjustment solution (such as ammonia), so as to achieve the purpose of controlling the pH value. Of course, due to the severely nonlinear nature of the pH value, the control method and setting parameters of the controller near the neutral point and at a pH of 7 (neutral point) are not the same. Therefore, the controller here is a complex controller that comprehensively considers the non-linear characteristics of the PH value and the valve adjustment characteristics. A simple PID regulator cannot complete the requirement. In addition, corresponding to the switching valve, the output of the controller is also a switching signal. In the control process of the PH value, it is firstly necessary to ensure that the frequency of the valve action is as small as possible within an acceptable range in order to extend the service life of the valve as much as possible. On the other hand, it is an indisputable fact that the valve is the most prone to failure in the entire regulating control loop. When the valve fails, ammonia may leak directly into the fermenter. Therefore, it is strictly independent and has redundancy. The configured pH alarm system is a must. It is better to have an emergency event processing system.
3.4 Dissolved Oxygen Concentration in Fermentation Process During the oxygen-consuming fermentation process, oxygen is used as a raw material for microbial growth. If oxygen supply is insufficient, the growth and metabolism of microorganisms will be inhibited. For this reason, a certain dissolved oxygen concentration must be maintained during the fermentation process. The main factors affecting the dissolved oxygen concentration are the amount of air supplied, the speed of the agitator, and the pressure in the fermenter. The control principle is shown in Fig. 3: Here a cascade control loop is adopted to eliminate the influence of pressure fluctuations in a timely manner while ensuring that the adjustment of the amount of steam to be passed meets the requirement of dissolved oxygen concentration. If the adjustment of the dissolved oxygen concentration is achieved by adjusting the rotational speed of the mixer, the situation is similar. As mentioned above, fluctuations in the pressure inside the fermenter have an influence on the dissolved oxygen concentration. Therefore, when the dissolved oxygen concentration control is achieved by adjusting the flow rate of the introduced air, this effect needs to be taken into consideration. If the fermenter pressure is automatically controlled, the fermenter pressure is considered constant. At present, the speed of the domestic fermenter stirrer is generally constant, so the dissolved oxygen concentration is controlled by adjusting the amount of air supplied. Of course, there are also simultaneous adjustments to the speed of the fermenter and the amount of air supplied.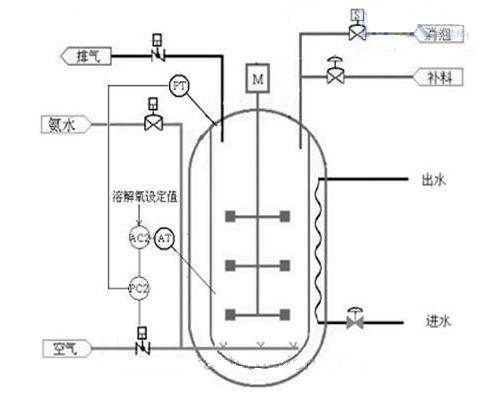
3.5 Defoaming control during fermentation In the early stage of fermentation, during the period of vigorous microbial growth, the feed liquid was fully loaded, and the stirring motor was started at full speed, and the air inflow reached a maximum. At this time, the fermentation broth floated very high, and if there is a slight carelessness, it may cause fluid escaping. At this point, even if defoamers are added, the foam must be reduced to prevent the broth from floating. The defoaming control usually adopts a two-position control method. When the liquid level of the fermentation liquid reaches a certain height, the antifoaming agent valve is automatically opened, and when the liquid level returns to normal, the antifoaming agent valve is automatically closed.
3.6 Feed control in the fermentation process During the semi-continuous fermentation process, as the fermentation progresses, the state of microbial growth and the state of biological metabolism are continuously supplemented with nutrients so that the microorganisms grow along the optimal growth trajectory. High-yield microbial metabolites. Due to the fact that microbial and metabolic conditions cannot be measured on-line, this supplementation is extremely difficult. The general fermentation industrial production process is based on a large number of experimental research results obtained by the laboratory to guide the industrial production of feed, and fermentation process technicians. According to the data from the laboratory laboratory tests, the feed rate was appropriately modified. This method may make good judgments for people with a lot of practical experience, but it is often unsatisfactory and cannot ensure that the fermentation process follows the most Excellent curves are performed and the best metabolites are not obtained. In view of the complexity of this fermentation process and the lack of information, the technical staff of the fermentation process and the automatic control personnel jointly studied and tried to find out better feeding methods and strategies. For example, the feed rate is controlled based on the release rate of carbon dioxide in the outlet gas, the amount of supplemental sugar is adjusted by a chemical element balance method, and the feed is controlled by a method that controls the respiratory quotient.
4, the system configuration for the specific characteristics of the biological fermentation process, the fermentation project selected distributed control system. The cost-effectiveness analysis uses the HT600 control system. The structure is shown in Figure 4. The control station is divided into a mashing plant, a fermentation plant, and a pharmaceutical plant. The operator station (Digivis) has three operator stations, one engineering station (CBF), and two Taiwan typewriters and operating stations are connected with a management network to facilitate monitoring of the entire plant's dynamics and data. A control network is used between the operating station and the control station to connect with industrial Ethernet. The control station is responsible for collecting, processing and completing the control functions of the on-site process data, and is connected to the operator station through a high-speed, reliable and open redundant system bus network, and can realize passive communication with other distributed control systems and upper-level information management systems. connection. The operating station/engineering station adopts a high-performance computer configuration and is equipped with a Windows operating system, which enables optimal control and safe operation of the biopharmaceutical process, generation of a friendly man-machine interface, real-time, safe and reliable supervision and control of the biopharmaceutical process. And optimization.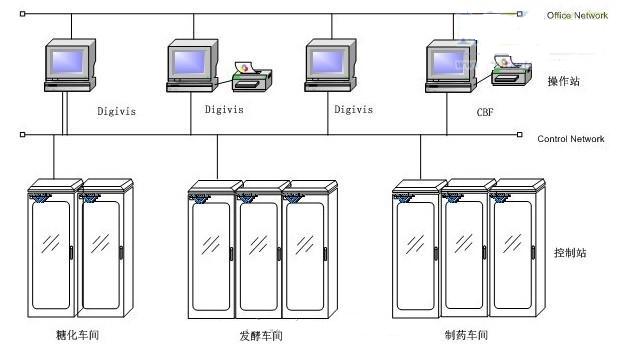
5. System Benefit Analysis Since the project was put into operation, the project has been operating stably with remarkable results, stable operation rate, single can production, and product quality. The labor intensity and raw material consumption of the workers have been greatly reduced, and at the same time, they have been ensured. The smooth and safe operation of the device. Directly improve the company's market competitiveness, for the company has brought very clear economic benefits. The successful commissioning of this project shows that the HT-600 system has high stability and reliability, but the configuration software has a huge structure and it is not easy for beginners to master. The main control indicators are as follows: fermentation tank temperature ± 0.2 °C; PH value ± 0.05; tank pressure ± 0.005Mpa, this indicator meets the requirements of fermentation control.
1 Introduction:
The use of secondary metabolism in the growth of microorganisms to obtain antibiotics in the pharmaceutical industry is a major creation of human biotechnology. This metabolic process is completed in the fermenter during industrial production. An in-depth study of the fermentation process will lay the foundation for the biochemical reaction—the design, operation and control of the fermenter. Therefore, it is one of the important contents of improving the level of biochemical engineering; biochemical reaction is a difficult point in biochemical technology. In the research and practical application, it needs not only microbial technology but also borrows chemical technology and modern measurement technology, computer technology and control technology. One. The microbial fermentation process is an extremely complex biochemical reaction process. For the operation of the fermenter, people used to rely on practical experience to conduct the operation. Due to the lack of measurement monitoring and control system of the fermentation process parameters, the fermentation product cost is high and the operating cost is high. The lack of competitiveness in the international market requires the optimization and control of fermentation tanks. Especially with the development of various technologies of computer control systems, distributed control systems have become more widely used in the pharmaceutical industry. This article mainly describes how to use distributed control systems to optimize the pharmaceutical control program.
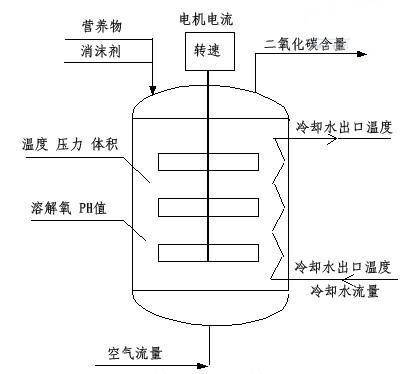
Figure 1 fermentation tank detection parameters
2, the process of fermentation and its characteristics The general oxygen-consuming fermentation tank system shown in Figure 1, which parameters to be measured can be divided into physical parameters, chemical parameters and biological parameters.
2.1 The physical parameters of the fermentation process are usually the fermentation tank temperature (T), the fermentation tank pressure (P), the fermentation liquid volume (V), the air flow (FA), the cooling water inlet and outlet temperature (T1¬ and T¬2) and the flow ( FW) stirring motor rotation speed (RMP), stirring motor current (I), foam height (H), etc. These physical parameters can be selectively selected to achieve automatic measurement according to different types of fermentation requirements.
2.2 Chemical parameters of the fermentation process:
The typical chemical parameters of the fermentation process are pH (PH) and dissolved oxygen (DO). These two parameters are very important for the growth of microorganisms and the formation of metabolites.
2.3 Fermentation process biological parameters:
Biological parameters typically include biomass respiratory metabolic parameters, biomass concentration, metabolite concentration, substrate concentration, and bio-specific growth rate, substrate consumption rate, and product formation rate. Regarding biological parameters, there are few real-time on-line measuring instruments in industrial production, both at home and abroad. It is precisely for these reasons that the control of the microbial fermentation process is more difficult than the general industrial production process.
3. Control of fermentation process With the rapid development of bio-industrial technology, its production equipment and scale are continuously expanding, the production process is strengthened, the requirements for automatic control technology are more and more urgent, the optimal control of the biochemical process is implemented, and production can be stabilized. Improve the yield, reduce consumption and increase efficiency. However, the microbial fermentation process is different from the general process industry. Because it involves the growth and reproduction process of living organisms, the mechanism is very complex, and various unpredictable oscillations often appear in the fermentation process, which brings about optimal control of the fermentation process. Great difficulty.
3.1 Conventional control of fermentation tank temperature For a given microorganism, it has an optimum growth temperature. If considered from the point of view of the enzyme kinetics, the best activity of the enzyme corresponds to the best temperature. Therefore, the control of the fermentation temperature in the microbial fermentation process is a very important environmental parameter for microbial growth and must be strictly controlled. The main factors affecting the fermentation temperature are the temperature of the microbial fermentation heat, the motor's stirring heat, and the cooling water itself.
The small-scale fermentation tank temperature control system is a single loop control scheme in which the fermentation tank temperature is controlled and the cooling water flow rate is a control parameter. For a large-scale fermentation tank system, the fermentation tank temperature is used as the main circuit, and the cooling water system is used. Cascade control or feedforward-feedback control scheme for the secondary loop.
(1) Single-loop PID control In the case of stable inlet water temperature, the temperature of the fermentation reaction tank is often controlled by a single loop PID. In the actual process of industrial fermentation process temperature control, due to changes in cooling water (or warm water) temperature, will affect the fermentation temperature control quality, the impact of the process is to first change the jacket temperature, and then change the temperature of the fermenter, only At this time, the controller senses the temperature difference and drives the regulator. Obviously, from the beginning of the disturbance to the action of the regulating valve, a large lag is required. To overcome these lags, cascade adjustment can be used.
(2) Cascade control The signals measured by T1 and T2 are combined into a control system. The output of TC1 is used as the reference value of the TC2 controller to form a cascade control system. Compared with single-loop control, cascade control has the following features:
(1) When the jacket temperature fluctuates due to some outside reason, the effect of TC2 will make this fluctuation overcome before it affects T1, so it is beneficial to ensure the control quality of T1. It can significantly improve the control characteristics of the fermenter and reduce the equivalent object lag.
(2) Two parameters can be taken into account to achieve "uniform control: When the main controller TC1 has a wider selection of proportionality, its output changes less. Because it is a given value of the sub-controller TC2, it makes secondary parameters. The change is also relatively small and relatively stable, so that the two main and auxiliary parameters can be kept within a certain range of fluctuations to meet the requirements of the process.
(3) The influence of non-linear characteristics such as the control valve can be eliminated: Since the control valve and a part of the object (sub-control object) are included in the sub-circuit, the nonlinear influence of the control valve is eliminated in the sub-ring.
(3) Feedforward-feedback control The cooling water temperature disturbance signal is applied to the regulating valve together with the output signal of the TC1 controller to form a feedforward-feedback control, so that the disturbance of the cooling water temperature change can be achieved. Quickly acting on the regulating valve, the regulating valve is also adjusted accordingly to eliminate this disturbance in time, but it should be noted that the feedforward compensator needs to have an accurate mathematical model as a basis.
3.2 Fermenter pressure The conventional control of the pressure change in the fermenter will cause the partial pressure of oxygen to change in the fermented liquid, which will affect the change of dissolved oxygen concentration. In addition, in order to prevent the fermentation product from being infected by bacteria, it is necessary to filter and sterilize the introduced compressed gas, and to ensure positive pressure in the fermentation tank so as to prevent the entrance of external untreated air and the like. The pressure that affects the fermenter is mainly the pressure change of the supplied sterile air. Usually the control of the pressure in the fermentor is controlled by adjusting the amount of exhaust gas. Generally, single-loop control can be used. The influence of the pressure change in the fermenter on the dissolved oxygen concentration is treated by the dissolved oxygen concentration control loop. Of course, the adjustment of the dissolved oxygen concentration will take into account the influence of the pressure in the tank.
3.3 pH Control During Fermentation PH is another important environmental parameter for microbial growth. In the fermentation process, it must be strictly controlled, otherwise it will seriously affect the metabolism of microorganisms and the synthesis of metabolites. In industrial production, if the PH value of fermentation broth is low and the ammonia nitrogen is also low, the PH value is increased by adding ammonia water, etc.; if the PH value is high and the ammonia nitrogen is low, ammonium sulfate or chlorination can be added. Ammonium; If the PH value and ammonia nitrogen are both high, in the early fermentation stage, the amount of sugar can be adjusted to increase. There are generally no other controls. Therefore, in the pH value control, the amount of the adjustment liquid must be strictly controlled and must not be excessive. As shown in FIG. 2, the pH value is controlled by the pH measuring electrode and the transmitter, the PH controller, the air switch, and the pneumatic switch valve. composition.
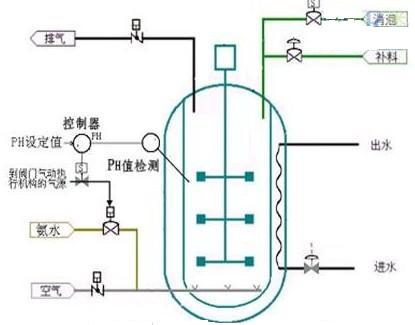
Figure 2 PH value control flowchart
Ammonia can be added to the fermentor through the sprinkler head. Of course, it is best to send it to the fermenter through the air duct together with the air, so that the ammonia can be fully distributed in the fermentation broth without causing high or low pH in the local area. . In order to avoid the defect that the general control valve has a leakage amount, in the PH control, the used valve is a commonly used on-off valve. According to the PH deviation signal, the controller calculates the switching period and the length of the opening and closing of the switching valve to control the amount of the adjustment solution (such as ammonia), so as to achieve the purpose of controlling the pH value. Of course, due to the severely nonlinear nature of the pH value, the control method and setting parameters of the controller near the neutral point and at a pH of 7 (neutral point) are not the same. Therefore, the controller here is a complex controller that comprehensively considers the non-linear characteristics of the PH value and the valve adjustment characteristics. A simple PID regulator cannot complete the requirement. In addition, corresponding to the switching valve, the output of the controller is also a switching signal. In the control process of the PH value, it is firstly necessary to ensure that the frequency of the valve action is as small as possible within an acceptable range in order to extend the service life of the valve as much as possible. On the other hand, it is an indisputable fact that the valve is the most prone to failure in the entire regulating control loop. When the valve fails, ammonia may leak directly into the fermenter. Therefore, it is strictly independent and has redundancy. The configured pH alarm system is a must. It is better to have an emergency event processing system.
3.4 Dissolved Oxygen Concentration in Fermentation Process During the oxygen-consuming fermentation process, oxygen is used as a raw material for microbial growth. If oxygen supply is insufficient, the growth and metabolism of microorganisms will be inhibited. For this reason, a certain dissolved oxygen concentration must be maintained during the fermentation process. The main factors affecting the dissolved oxygen concentration are the amount of air supplied, the speed of the agitator, and the pressure in the fermenter. The control principle is shown in Fig. 3: Here a cascade control loop is adopted to eliminate the influence of pressure fluctuations in a timely manner while ensuring that the adjustment of the amount of steam to be passed meets the requirement of dissolved oxygen concentration. If the adjustment of the dissolved oxygen concentration is achieved by adjusting the rotational speed of the mixer, the situation is similar. As mentioned above, fluctuations in the pressure inside the fermenter have an influence on the dissolved oxygen concentration. Therefore, when the dissolved oxygen concentration control is achieved by adjusting the flow rate of the introduced air, this effect needs to be taken into consideration. If the fermenter pressure is automatically controlled, the fermenter pressure is considered constant. At present, the speed of the domestic fermenter stirrer is generally constant, so the dissolved oxygen concentration is controlled by adjusting the amount of air supplied. Of course, there are also simultaneous adjustments to the speed of the fermenter and the amount of air supplied.
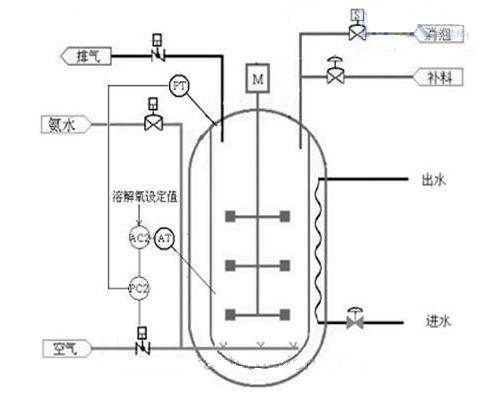
Figure 3 Cascade control loop
3.5 Defoaming control during fermentation In the early stage of fermentation, during the period of vigorous microbial growth, the feed liquid was fully loaded, and the stirring motor was started at full speed, and the air inflow reached a maximum. At this time, the fermentation broth floated very high, and if there is a slight carelessness, it may cause fluid escaping. At this point, even if defoamers are added, the foam must be reduced to prevent the broth from floating. The defoaming control usually adopts a two-position control method. When the liquid level of the fermentation liquid reaches a certain height, the antifoaming agent valve is automatically opened, and when the liquid level returns to normal, the antifoaming agent valve is automatically closed.
3.6 Feed control in the fermentation process During the semi-continuous fermentation process, as the fermentation progresses, the state of microbial growth and the state of biological metabolism are continuously supplemented with nutrients so that the microorganisms grow along the optimal growth trajectory. High-yield microbial metabolites. Due to the fact that microbial and metabolic conditions cannot be measured on-line, this supplementation is extremely difficult. The general fermentation industrial production process is based on a large number of experimental research results obtained by the laboratory to guide the industrial production of feed, and fermentation process technicians. According to the data from the laboratory laboratory tests, the feed rate was appropriately modified. This method may make good judgments for people with a lot of practical experience, but it is often unsatisfactory and cannot ensure that the fermentation process follows the most Excellent curves are performed and the best metabolites are not obtained. In view of the complexity of this fermentation process and the lack of information, the technical staff of the fermentation process and the automatic control personnel jointly studied and tried to find out better feeding methods and strategies. For example, the feed rate is controlled based on the release rate of carbon dioxide in the outlet gas, the amount of supplemental sugar is adjusted by a chemical element balance method, and the feed is controlled by a method that controls the respiratory quotient.
4, the system configuration for the specific characteristics of the biological fermentation process, the fermentation project selected distributed control system. The cost-effectiveness analysis uses the HT600 control system. The structure is shown in Figure 4. The control station is divided into a mashing plant, a fermentation plant, and a pharmaceutical plant. The operator station (Digivis) has three operator stations, one engineering station (CBF), and two Taiwan typewriters and operating stations are connected with a management network to facilitate monitoring of the entire plant's dynamics and data. A control network is used between the operating station and the control station to connect with industrial Ethernet. The control station is responsible for collecting, processing and completing the control functions of the on-site process data, and is connected to the operator station through a high-speed, reliable and open redundant system bus network, and can realize passive communication with other distributed control systems and upper-level information management systems. connection. The operating station/engineering station adopts a high-performance computer configuration and is equipped with a Windows operating system, which enables optimal control and safe operation of the biopharmaceutical process, generation of a friendly man-machine interface, real-time, safe and reliable supervision and control of the biopharmaceutical process. And optimization.
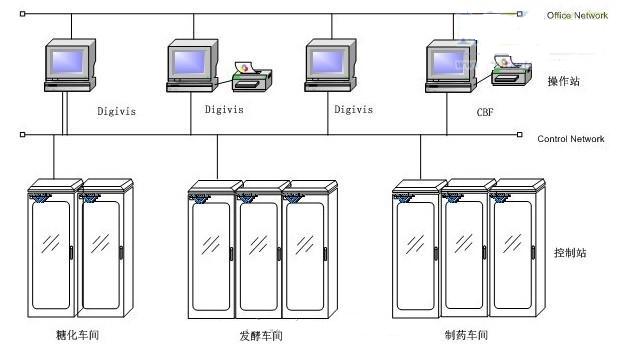
Figure 4 system structure
5. System Benefit Analysis Since the project was put into operation, the project has been operating stably with remarkable results, stable operation rate, single can production, and product quality. The labor intensity and raw material consumption of the workers have been greatly reduced, and at the same time, they have been ensured. The smooth and safe operation of the device. Directly improve the company's market competitiveness, for the company has brought very clear economic benefits. The successful commissioning of this project shows that the HT-600 system has high stability and reliability, but the configuration software has a huge structure and it is not easy for beginners to master. The main control indicators are as follows: fermentation tank temperature ± 0.2 °C; PH value ± 0.05; tank pressure ± 0.005Mpa, this indicator meets the requirements of fermentation control.